Three-DoF Oscilatory Rail Constrained Helicopter
-
Three-DoF Oscilatory Rail Constrained Helicopter -
the future of avionics education.
The Three-DoF Oscilatory Rail Constrained Helicopter (TORCH) is a never-before-seen modeling and simulation tool aimed at supplementing avionics education. This groundbreaking work is currently under review for AIAA technical paper publication.
Check out the extended abstract!
My Role
As the team lead for the TORCH project, I oversee project coordination, facilitate collaboration, and guide the team in developing innovative solutions, ensuring alignment with technical, budgetary, and timeline requirements.
-
I played a key technical role in the TORCH platform by not only designing, testing, and optimizing the drone, structural frame, and pulley-counterweight system but also by focusing on assembly and integration. Lately, my work has centered on hands-on tasks such as soldering circuits and using 3D printing for rapid prototyping, which have been critical in expediting component development. In addition, I tackle troubleshooting challenges and solve technical issues that could otherwise delay the team's progress, ensuring smooth integration and robust performance throughout the project. As team lead, I also am responsible for task delegation and serve as the POC between the team and out stakeholders
-
I enhanced assembly and integration through hands-on soldering and 3D printing for rapid prototyping, troubleshooting issues that could hinder overall team performance. Additionally, I integrated static analyses for the pulley-counterweight system to refine its optimal design, and leveraged data-driven techniques from my AeroScale project to test thrust and torque on the propeller-motor system—comparing various propeller sizes and validating the 3-inch tri-blade selection. Also, I ensured rigorous technical documentation by adhering to AIAA manuscript guidelines using Microsoft Office Suite, and I employed SolidWorks for detailed CAD modeling and finite element analysis of the structural frame.
-
My leadership ensured the team successfully reached key design milestones. With the team’s work in modeling and analyses, TORCH is now ready to be manufactured. Additionally, our work already helped with our own understanding of flight dynamics and control. This result is evidence that our project will serve its purpose — to supplement avionics education.
Project Details
The TORCH platform simulates 3-DoF using a system of linear guide rails, pullies, and counterweights. Combined with MATLAB/Simulink, students will use TORCH to learn avionic control algorithms through an intuitive step-by-step process
-
The structural frame is constructed from 40x40 aluminum T-slot extrusions and carbon-steel linear guide rails. A pulley-counterweight system balances the weight of the rails, allowing the drone to carry only its own load. Key subsystems include cable management, sensor housings, a pitch-angle indexing plate, and safety features like plexiglass shielding and limit switches. The custom-designed drone has been optimized to meet performance and educational requirements. This design allows for the simulation of movement in three degrees of freedom.
-
TORCH's software subsystem enables students to design, implement, and test control algorithms using MATLAB/Simulink and SPAARO, a control algorithm designed by LAGER (the laboratory for autonomy, GNC, and estimation research) at UA. The platform collects real-time performance data from sensors for analysis. For versatility, the system can be run on any PC that supports Linux. Currently, the software team is designing a user interface that will allow for a streamlined operation process.
-
I’m super thankful for the support of the team - Madeline Bunch, Luca Hallenbeck, Zach Herring, Arden Markin, and Zac Powers. Their excellence has made my role seamless and rewarding! Furthermore, special thanks to Dr. Jordan Larson for devising and assigning our team this project, and for his invaluable leadership and guidance!
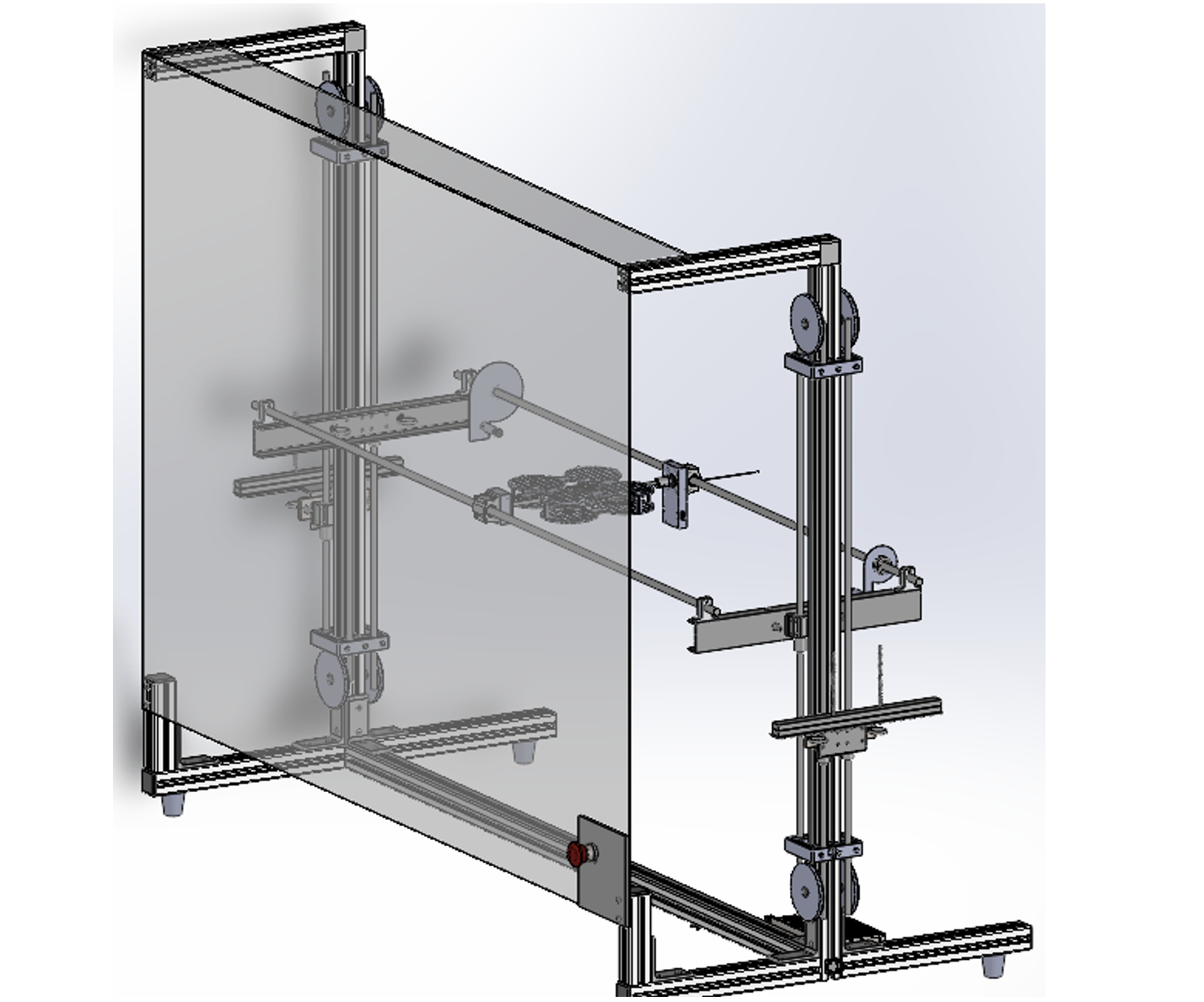
